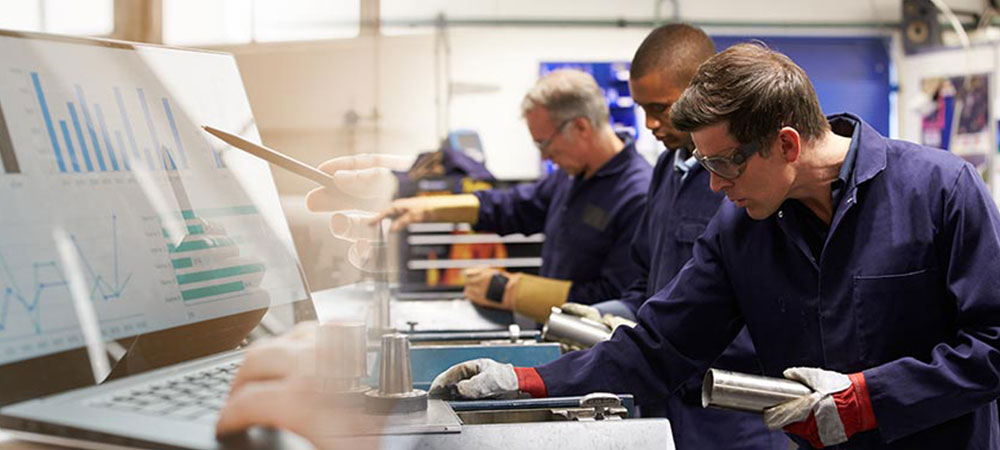
Un sistema informativo per gestire il miglioramento continuo
L’attività di miglioramento continuo all’interno di un’azienda viene normalmente divisa in miglioramento focalizzato e miglioramento sistematico. Oggi è invalso l’uso di riferirsi al primo attraverso il termine Kai-zen e al secondo con una serie di sigle riferite alle varie metodologie (World Class, Six Sigma, ecc.) che trovano una sintesi nell’espressione “excellence system”.
L’approccio Kaizen, diffuso con il Toyota Production System o TPS, è sempre stato legato ad una gestione cartacea delle varie fasi di questa attività, come da tradizione giapponese. Il Kaizen, infatti, viene solitamente gestito attraverso un tabellone sul quale vengono man mano affissi i documenti che il kaizen team elabora nelle riunioni progettuali necessarie all’implementazione delle varie attività. Sul tabellone prendono posto quindi i moduli dei diversi strumenti, quali 5w+1h, 4M Ishikawa, 5 whys, carte di controllo, ecc., che vengono elaborati durante lo sviluppo del progetto del singolo miglioramento.
Fino a quando questo approccio riguarda un solo sito produttivo, la metodologia classica è sufficiente a permettere un controllo “a vista” di quanto viene realizzato dai diversi team. L’introduzione, il consolidamento e l’estensione di questo approccio all’interno di una grande azienda con diversi siti produttivi richiede però il supporto di un sistema informativo per la gestione remota dell’attività e per l’individuazione e la diffusione delle best practice.
In Maserati, FCA e Magneti Marelli le prime applicazioni per gestire il miglioramento continuo su larga scala
La prima applicazione per la gestione su larga scala dei kaizen è stata realizzata da Exagogica nel 2014 per FCA all’interno dell’applicazione PD online. I workflow dell’applicazione consentiva sostanzialmente di gestire i cosiddetti quick kaizen, ovvero quelli che nella metodologia WCM non avevano la necessità di definire un team e potevano essere svolti in autonomia da un singolo operaio.
L’applicazione, sviluppata inizialmente all’interno dello stabilimento Maserati di Grugliasco, ebbe un rilevante successo, diffondendosi fra gli stabilimenti italiani del gruppo FIAT e arrivando a gestire oltre 200.00 proposte di miglioramento e 7.000 kaizen. Di particolare rilevanza nell’applicazione erano la reportistica dei livelli di propositività e dei saving generati da ciascun operaio, sistema di report che consentiva di gestire i piani di recognition and rewarding associati allo sviluppo del coinvolgimento degli operatori. Il sistema consentiva inoltre di gestire il catalogo di tutti i miglioramenti realizzati, offrendo strumenti per effettuare ricerche per componente, tipologia di processo, caratteristiche del problema e della soluzione implementata.
Successivamente al sistema customizzato per FCA, Exagogica ha sviluppato il sistema per la gestione del miglioramento continuo denominato Compass Room per Magneti Marelli. In questo sistema, nato per unificare la gestione dei pilastri Cost Deployment, Focused Improvement e People Development, abbiamo questa volta implementato i principali strumenti necessari per la gestione dei kaizen su larga scala.
In particolare il sistema da noi realizzato offriva la gestione della knowledge inventory per la selezione dei migliori team leader e team member, la previsione del workload per evitare sovraccarichi di lavoro, la verifica delle competenze e la pianificazione della formazione on the job attraverso la skill matrix, l’uso dei dati sui saving nei progetti per la staff classification e l’individuazione degli exceptional people.
Grazie all’esperienza sviluppata sui questi grandi progetti di customizzazione siamo riusciti a introdurre man mano logiche e strumenti del ciclo di Deming all’interno dei nostri moduli software standard. In particolare nel 2017 abbiamo rilasciato la prima versione del modulo di Panoptikon 2.3 EHS Management con la digitalizzazione delle 4 fasi del ciclo di Deming (Plan, Do, Check, Act) e di tutti gli strumenti collegati. Il modulo, già utilizzato in Elica S.p.A., è stato poi aggiornato nel 2019 e adottato da Denso su 18 stabilimenti della business line Tec.
Con “Kaizen management” una gestione più semplice e completa di tutte le attività di lean manufacturing
Sempre nel 2019 abbiamo completato la prima versione del modulo 2.5 Kaizen management, che offre finalmente un sistema integrato e completo per la gestione su larga scala delle attività di lean manufacturing incentrate sulla metodologia Kaizen.
Questo modulo, alla base delle nostre attuali offerte per la gestione delle Blue room e Compass room, consente la raccolta delle proposte di miglioramento focalizzato, al gestione dell’analisi di fattibilità, la scelta del team leader e dei team member, la schedulazione del progetto. Per la fase di implementazione, il sistema consente la gestione dei forecast di spesa e risparmio, oltre alla consuntivazione delle attività ed al caricamento dei documenti relativi.
La fase di verifica dell’impatto economico del progetto è assistita da strumenti che agevolano il controllo dell’applicazione dei costi standard e la verifica mensile degli scostamenti. Al termine del processo, il sistema consente l’archiviazione del progetto, la sua diffusione come best practice e anche la programmazione della sua diffusione all’interno dell’organizzazione su progetti similari.
“Panoptikon Kaizen Management” è oggi la soluzione ideale per gestire la lean organization all’interno di organizzazioni di ogni genere.
Alessandro Obino, CEO Exagogica
© Riproduzione riservata