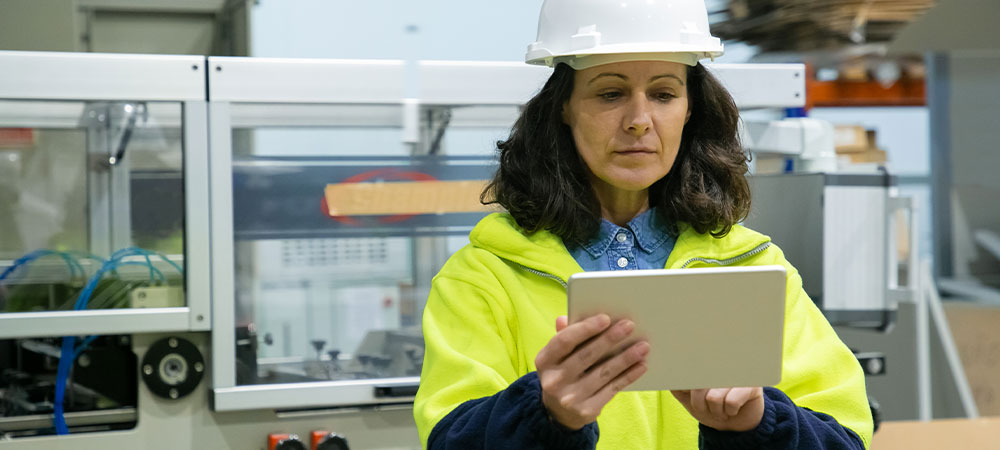
How to evoke the tremendous hidden power of checklists?
The checklist is one of the simplest and, at the same time, most powerful tools within a large organization. The problem is that in many industries it is used little and badly. It is a pity, first of all, that it is used outside the process of collecting and analyzing information from the field of which it should instead be an integral part.
The checklist is nothing more than the list of conditions to be verified for a self-inspection conducted directly by the worker or by the manager of a processing area. It can be used to check that everything is compliant before starting the work shift, to check the quality of a process or product, or to check that the operating conditions of a processing area guarantee the safety and health of workers. Very often, however, it is experienced by workers as a waste of time and, therefore, disregarded. Not filled in or, which is even worse, summarily filled in by indicating ex officio that everything is in order.
Why does this happen?
Based on my experience, the reasons are basically two: because the conditions to be verified in the self-inspections are often generic and not always applicable to the reality of the area subject to the verification activity and because the problems detected are not implemented by the management of the production, making the activity itself essentially useless.
The execution of self-inspection activities within the plants is really a fundamental element of lean production, since it is one of the tools with which each worker becomes aware of the various aspects of the organization of one’s work and, for this reason, is ” autonomous “(Jidoka), that is, becomes a part of the organizational aspects so that can make one’s contribution to improve them for one’s well-being and for improving the overall efficiency of the system.
In order for a self-inspection activity to make sense, it cannot be entrusted to the classic sheets of paper to be filled because the paper has two major defects: once printed it cannot be changed and, once written, it must be subject to a coding (data entry) so that the information contained in sheets of paper can be analyzed. So it happens that the checklists that are compiled, contain items that are “not applicable” (and this should never happen if you want the worker who compiles them to keep their motivation to do it!). In addition, you end up with packages and packages of checklists that the area manager should read and transcribe on a computer every day in order to take advantage of that activity, which of course will never be done!
In essence, the “prepackaged” paper checklists are a convenient and quick way out for an activity that actually requires a higher management cost. At the same time they are the gravestone on the process of which they should be part.
My experience in the plant has led me numerous times to face this situation. I remember seeing the first checklist packs on the UTE tables (sub-units) of the FCA plant in Mirafiori during my first consultations on World Class Manufacturing in 2008. From that moment on, every time I entered a production site, I learned to recognize the piles of sheets that lay on the tables and in the cabinets of supervisors of various levels. Someone had filled them out, investing time for work anyway, and nobody would ever read them.
Over time I have had the opportunity to work on some of these checklists, in different contexts. At Fiat Powertrain in Verrone in 2012 I worked on the quality controls preparatory to the ISO/ TS 16949 audits. Subsequently I had the opportunity to work, again in FCA, on SMAT (Safety and Environment) and in 2015 we set up the management of the reports deriving from internal inspections for Elica SpA
When in 2017 we received the request from Denso TEC to help them manage the Safety Inspection process for the Poirino plant,
We understood that it was a good opportunity to finally create an information system that would support the whole self-inspection process, without be afraid of managing complexity and trying to bring out all the benefits that are present in it.
Our client’s need was to manage a very complex questionnaire (62 conditions to be verified at each inspection), which had to be repeated weekly in each work area and which often had conditions not applicable to the area itself. Furthermore, Denso wanted to eliminate the waste given by the double data entry (the questionnaire was printed and executed on paper, then transcribed in excel and the reports were made with complex pivot tables).
In addition to digitizing the checklists, it was necessary to keep the scoring system connected to the execution of self-inspections, to keep track of the execution day in order to verify delays and defaults and, last but not least, the management of the plant wanted all the found compliance automatically triggered a search for the root cause and the application of the related countermeasures within the management program of the Health, Safety and Environment continuous improvement system we developed the previous year.
Faced with a challenge of this kind, Exagogica has decided not to create a simple utility for making checklists on mobile devices, but has created a module that is fully programmable and integrated into the Panoptikon system, precisely to allow the creation of an automatic Unsafe Condition reporting starting from a non-compliance found during the self-inspection phase.
The adoption of our solution for Inspection Management has allowed Denso TEC to save a lot of time in the execution and analysis of inspections, increasing the execution rate and the number of countermeasures produced by the reports collected. The programming system, in fact, allows to create different types of inspection, each with its own scoring system. Each checklist, then, can be associated with a specific area of the plant, defining which conditions are applicable and which are not, in order to deliver a specific checklist for its area to the operator. The assignment of the activities is done through a scheduler that notifies the operator when the inspection is assigned to him and reminds him of the day scheduled for execution.
The inspection activity can be performed on a mobile system (the operator receives a notification from which activates the inspection module directly, without a necessity to access the system). The monitoring system allows to keep all the activity under control, recalling those who are late and making all necessary statistical analyzes on the scores achieved.
The most relevant aspect, however, is precisely the system’s ability to generate Unsafe Condition safety signals based on the type of non-compliance found, without the operator having to add any other information.
This feature led the system to be adopted not only by the Poirino plant, but by the entire Denso TEC Business Line, which now uses it in its 18 plants worldwide.
Alessandro Obino, CEO Exagogica
© All rights reserved