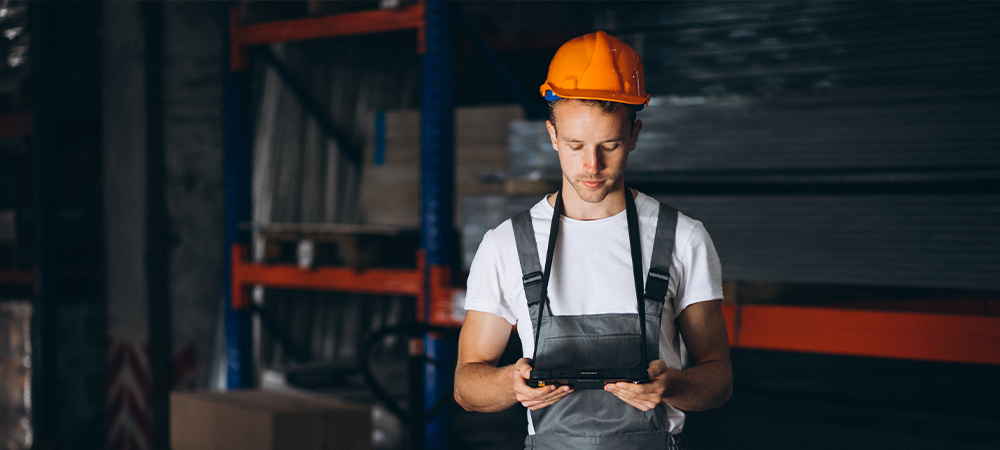
La gestione globale di Salute e Sicurezza a portata di mouse
La gestione di Salute e Sicurezza all’interno delle grandi organizzazioni industriali richiede un approccio duplice.
Da una parte è necessario che i responsabili facciano rispettare le norme di legge e i regolamenti specifici di cui si è dotata l’organizzazione. Possiamo definire questo approccio come “top-down”, ovvero dall’alto verso il basso. Dall’altra è opportuno che coloro che vivono realmente la fabbrica tutti i giorni segnalino i pericoli reali e potenziali, in modo che chi si occupa di gestire la produzione possa costantemente migliorare le misure organizzative.Possiamo definire questo approccio come “bottom-up”, ovvero dal basso verso l’alto.
Il primo approccio è obbligatorio per legge e sostanzialmente non richiede la gestione di grandi quantità di informazioni. È un approccio “qualitativo”, in cui la comunicazione è effettuata tramite documenti ufficiali (piani, disposizioni, ecc.) e ordini di servizio. Il suo fine principale non è tanto il miglioramento delle reali condizioni di lavoro, quanto ottemperare alle disposizioni obbligatorie di legge, in maniera da non avere problemi con gli ispettori dei servizi sanitari nazionali. Lo so che non dovrei scrivere una cosa di questo genere, ma chiunque abbia lavorato in ambito industriale, sa benissimo di cosa sto parlando. Il secondo approccio, invece, non è obbligatorio, ma è talmente importante che le aziende hanno fatto di tutto per renderlo uno standard, obbligandosi a vicenda a rispettare il principio di raccogliere costantemente informazioni dal basso, verificarle, individuare nuove modalità per diminuire i rischi di qualunque tipo e valutare le modifiche introdotte per capire se è possibile fare ancora meglio.
Il principio è quello del miglioramento continuo ed è alla base di ciascun Sistema di gestione della Sicurezza sul lavoro (SGSL).
Il principale metodo che le aziende hanno trovato per obbligarsi l’una con l’altra ad applicare questo principio per quanto riguarda la salute e la sicurezza dei lavoratori è stata la richiesta di certificazione alla norma internazionale ISO 18001 (OHSAS – Occupational Health and Safety Assessment Series) che i principali produttori fanno ai loro fornitori e questi riversano a cascata sulla loro filiera.
La stessa cosa è stata fatta per la salute e la sicurezza dell’ambiente, attraverso la reciproca richiesta di adesione alla norma ISO 14001 e la creazione di un Sistema di Gestione Ambientale (SGA). Entrambi questi sistemi, poi, sono stati spesso inseriti all’interno di norme più specifiche e restrittive che riguardano unparticolare gruppo industriale, come ad esempio il World Class Manufacturing che prevede dei sistemi di miglioramento continuo molto avanzati sia per il pilastro Safety che per il pilastro Environment.
La nascita di questo approccio “dal basso” non è poi una novità così recente. Già negli anni ’60, presso lo stabilimento FIAT di Mirafiori, erano nati i “gruppi omogenei” in cui operai e capofficina discutevano insieme i possibili miglioramenti alla salubrità delle zone di lavoro. Nel 2007 mi era capitato di lavorare alla produzione di un documentario che raccoglievano i ricordi di Ivar Oddone, il medico del lavoro che aveva impostato le mappe in cui gli operai segnalavano i possibili rischi in base alla loro esperienza sensoriale (rumori, odori, percezione visiva di pericoli, ecc.). Scoprire che già tanti anni prima simili metodologie erano state applicate in quella che, all’epoca, era la più grande fabbrica d’Europa, mi aveva veramente stupito.
Così, quando nel 2008 mi è stato chiesto di fornire agli impiegati dello stesso stabilimento un sistema di formazione a distanza relativo agli obblighi della norma ISO 14001 sul miglioramento continuo ambientale, ho realizzato che lo stesso approccio, a distanza di diversi decenni dominati in occidente da un rigido dirigismo tecnocratico, era alla base delle più moderne pratiche di miglioramento continuo in materia di Salute e Sicurezza sui luoghi di lavoro e di Ambiente.
La prima richiesta di implementazione di un sistema software per la raccolta e l’analisi dei dati relativa a Safety e Environment mi è poi arrivata nel 2014 da Elica S.p.A., l’azienda italiana leader mondiale nella produzione di cappe di aspirazione per cucina. La strada scelta da Exagogica per fornire lo strumento necessario a coordinare l’attività in tutti gli stabilimenti italiani è stata quella di sviluppare uno specifico modulo del nostro sistema Panoptikon. Questo ha consentito di creare un sistema di raccolta dei dati sfruttando la mappatura delle linee di produzione già presente nei moduli di gestione dell’impiego della manodopera.
Il modulo HSE è entrato in uso in Elica l’anno successivo e da allora viene utilizzato per gestire la raccolta di tutte le segnalazioni e, soprattutto, per elaborare gli indicatori di rischio delle varie aree di produzione, tramite gli strumenti della Heinrich Pyramid e della S matrix.
Lo strumento già dall’anno successivo è stato adottato dal principale stabilimento italiano della Denso, al multinazionale automotive giapponese del gruppo Toyota. Per l’implementazione in Denso, oltre ai normali sviluppi previsti nella roadmap di prodotto, abbiamo implementato un sofisticato sistema di pianificazione, esecuzione e analisi degli audit interni.
Nel 2018 Exagogica ha poi ricevuto da Denso TEC la richiesta di realizzare uno strumento con cui gestire le attività di Health and Safety a livello globale nei suoi 18 stabilimenti. Partendo dai moduli già implementati, abbiamo effettuato una customizzazione che rende il sistema di Denso TEC una best practice per l’implementazione di un sistema di gestione della sicurezza basato sull’approccio del miglioramento continuo.
Il sistema fornito da Exagogica, infatti, consente una facile segnalazione dei safety tag (unsafe act e unsafe condition) sia per segnalazione spontanea che a seguito dell’esecuzione di una ispezione o di un audit di sicurezza. I tag vengono analizzati statisticamente in maniera da definire le zone di maggior rischio e sulle quali approfondire le attività di analisi per migliorare le condizioni di sicurezza. Il Sistema implementato prevede anche la gestione di accident, first aid, near miss, ergonomic injuries, infortuni in itinere, che sono oggetto di un’analisi approfondita per la ricerca della causa radice attraverso l’applicazione guidata passo passo dei metodi tradizionali di analisi: 5W+1H, Ishikawa, 5Whys. Il procedimento di analisi è integrato con l’applicazione delle contromisure.Una volta individuate, queste vengono trasmesse agli incaricati che devono applicarle nella propria specifica area di produzione e la loro implementazione viene tracciata e monitorata attraverso il sistema.
Il modulo HSE di Exagogica consente inoltre la gestione della trasversalizzazione, ovvero della programmazione dell’implementazione delle contromisure in aree simili a quella in cui sono state inizialmente introdotte, così come permette una facile gestione delle best practice, che vengono condivise a livello globale fra tutti gli stabilimenti del gruppo.
Il vero punto di forza del sistema consiste però nella gestione dei KPI, i Key Performance Indicator relativi alla sicurezza, che vengono aggregati automaticamente dal singolo reparto fino alle country e ai valori complessivi. La gestione totalmente automatizzata di questi valori, che vengono derivati dall’attività transazionale di tutti gli operatori coinvolti, consente la piena e reale implementazione di un sistema di miglioramento continuo della sicurezza basato sulla raccolta costante delle informazioni di chi vive ogni giorno la vita dello stabilimento.
Il sistema che abbiamo implementato in Denso TEC, dopo alcuni mesi di rodaggio, è diventato standard del gruppo nel luglio del 2019. Da quel momento assicura il costante aumento degli standard di sicurezza per oltre 8.000 operai e questa per me non è solo una soddisfazione legata alla conclusione di un lungo percorso di ricerca, ma un reale motivo di orgoglio per l’utilizzo del software che abbiamo realizzato.
Alessandro Obino, CEO Exagogica
All rights reserved