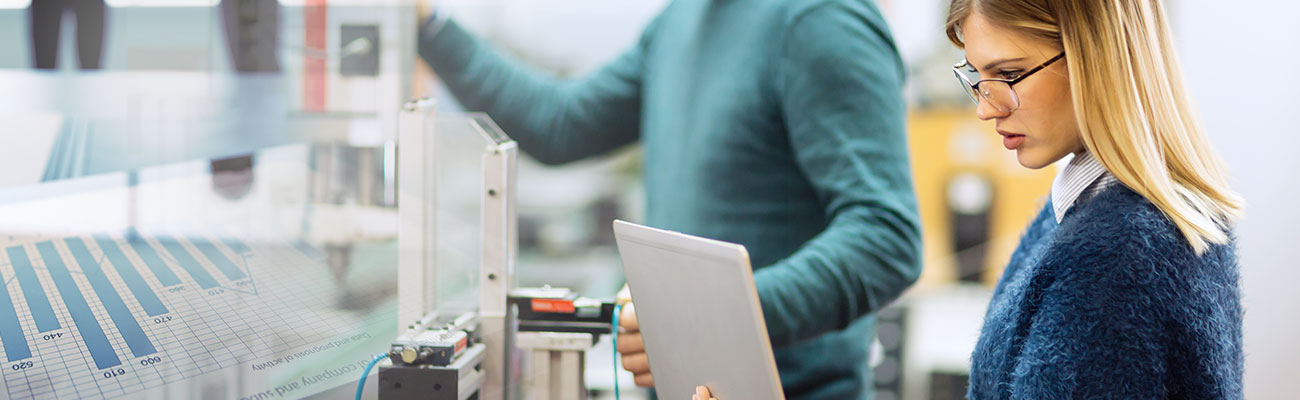
Process Manager: a complete system for Health, Safety and Environment indicators management
Process Manager is the Exagogica framework used to implement Health and Safety Management Systems (OHSAS ISO 18001), Environment (ISO 14001) and Quality (ISO-TS 16949 and similar). It is also used to implement continuous improvement management systems for Lean Organization (Best Practice, Kaizen management, TPS).
Process Manager has been adopted by some major manufacturing companies and is employed by each of them in dozens of factories around the world. Process Manager is a powerful and flexible tool, characterized by a modular structure and useful to cover multiple functional areas.
Process mapping
Process mapping is the basis of all Process Manager functions. To allow a faithful representation of the production process, we have in fact provided the features to manage the entire structure of a company with different business lines and different geographical regions.
In addition to the extension of the represented process, the strength of Process Manager lies in its flexibility. The process operations, in fact, can be associated with different workstations depending on the configuration of the production unit. This allows you to manage inspections and analyses, adapting them immediately to the production requirements for the plant.
Operator Readiness
A simple and quick check of the operators’ availability on the assigned workstations is essential to guarantee the quality of production and prevent non-conformities of any kind. Especially when there is a need to choose between different production configurations.
Thanks to the Operator Readiness module, Process Manager tracks the work capacity of employees on each individual production operation. it also manages compulsory training, on-the-job training, renewal of licenses and qualifications, physical suitability and sanitary exclusions. All this very quickly thanks to the possibility of associating operations with similar characteristics.
With the ability to manage different production configurations by associating individual operations with different possible workstations, Operator Readiness allows you to immediately know which operators have the suitability, qualifications and skills to work in them.
Inspection management
The same flexibility of Operator Readiness can be found in the Inspection Management module, created to configure, define, program, execute and analyze compliance inspections within a production plant. Inspection Management makes it possible to determine various types of internal audits, define observation checklists and scoring systems, declare the authorized inspectors and for which areas of the plant.
Each inspector is assigned of scheduled inspections, so that on the scheduled day he receives a notification and can proceed with the required activities by filling out the checklists on his computer or mobile device.
When non-compliance is detected during the inspection, the system automatically generates a recovery action that will be managed within the Health Safety Environment module, or within the Continuous Improvement module. The data collected in the inspections, on the other hand, will flow into the reporting of the Inspection Management module which will thus allow you to easily monitor the situation of each area of the plant and the activity of each individual inspector.
Health Safety Environment
A complete system for Health, Safety and Environment indicators management within the factories of an industrial group: Health Safety Environment allows you to easily collect operator reports on Unsafe act, Unsafe condition, Near miss and Accident and to manage all reaction activities ranging from root cause analysis to countermeasures implementation check.
The analysis of aggregate indicators on various levels (from the production unit to the group, passing through factories, geographic regions and business lines) and the dissemination of best practices complete a this added value tool for sanitary and environmental risk prevention.
Continuous improvement
The systematic management of continuous improvement activities (Kaizen Management) is one of the foundations of the Toyota Production System and of all the methodologies derived (Lean production).
Exagogica Process Manager offers an agile and powerful solution to manage all the phases of an improvement projects, from their selection and planning to implementation and verification of economic impact. Furthermore, with Process Manager, it is also easy to manage the analysis of aggregate data to identify the best types of projects, the best methods and the most effective people in the fight against losses and waste.
Due to these characteristics and the high possibility of customization, Exagogica Process Manager has been used in the last ten years by several large industrial groups to manage their excellence system programs in the manufacturing industry and in the R&D sector.
Do you want to know more about Exagogica and discover all its solutions?